Thursday, July 20, 2006
A reality show I could REALLY watch
So who do I call about this?
Wednesday, July 19, 2006
Backstrap weaving, the next generation

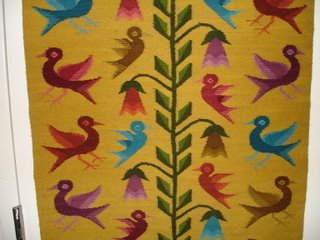
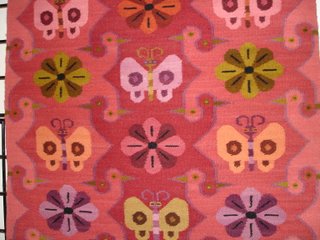

(as near as I can figure, 2 eyes and a nose)


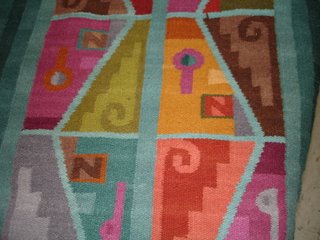
So much stuff, and by the end of the 3 days he had 2 pieces left. People were calling friends and spouses to COME AND LOOK AT THIS AMAZING STUFF. He is going to apply to be at MDSW next year! Bring money!! The interpreter said they never expected to sell anything to the class. He was supposed to take these works to the Textile Museum.

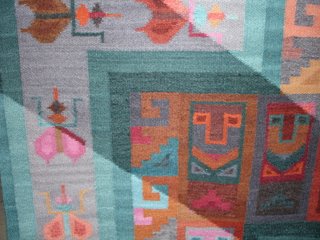
All the colors in this (below) except for the blues are derived from the masicopa plant (again, questionable spelling)
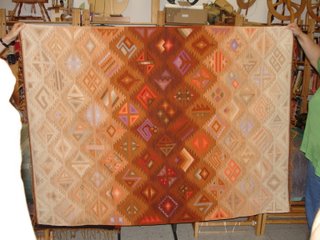

Alex's family collect all their own dye plants. He showed a little DVD about his family and their business. They go to the wool market to buy their wool and alpaca. His mother fluffs open the locks before handspinning on a drop spindle. All the wool is spun by his mother or aunt on drop spindles. They spin singles. They have never seen a spinning wheel, and Alex saw this first one at Springwater Fiber Workshop. After the wool is spun and skeined, it is washed in large washtubs: the women stomp on it much like stomping on grapes. Then they beat it against the stone wall to "spin dry" most of the water out of it. (the subtitle here actually says "spin dry") Dyeing is done by the men on the patio in large cauldrons over a wood fire. The warping of the backstrap looms was shown in a slide show on a CD.
First I will show you the parts of the backstrap loom and then I'll describe how it was set up. Alex and his cousin prepared these for us: it took them 6-8 hours per loom. This shows the strap that would go around your hips. Alex was much concerned that the strap would cause us pain, forgetting how well cushioned we Americans are (he is very thin). The stick is used both to form the shed to pass the yarn through, and to beat with. The black strings are the heddles, looped around every other string.
Another look at the heddles
This stick is behind the heddles. Note the brown rope. It contains all the threads that do not have a heddle. Note also at the top of the picture, how overspun the yarn is,
This shows how the warp threads are attached to the loom: they are "sewn" on. If you look carefully against the wood, you can see a little bit of brown rope next to the white rope. The brown rope is placed inside the warp threads and it is actually what gets sewn on, otherwise you'd have to sew every thread on. close-up of the rope
close-up of the heddles. They are "figure-8'd" around every other thread and the top wooden bar. The 2 bars are lashed together to keep the heddles in place.
showing the sewing at the other end
To warp a loom: they had 2 vertical poles set in cement in the ground. The warp thread is passed from one end to the other, with a figure 8 in the middle to keep the cross. The colored threads are warped on in the proper place (i.e.: in the order needed) A rope is placed inside the warped yarn, and this rope is stitched to the loom, as above. It looks like one pass around the loom stick every 1/4-1/2 inch. This is done at both ends. Then the heddles are threaded. (This was not shown) Some way must be utilized to keep the heddle threads separate from the other threads, because the other threads are enclosed by the brown rope. I would guess that a shed stick is used, and every thread that has a heddle around it is on the top of the stick, and the un-heddled threads, if you will, are on the bottom. It would then be simple to enclose the unheddled threads with a rope. Now let's look at how the loom works.
You can see Alex pulling down on the rope encasing the unheddled threads while lifting the wooden bars that have the heddles attached. Here he is looking to see if he has a clear shed to pass the stick through. You don't want any crossed threads, or they'll break
Here he is picking up the design. This was my big surprise. I thought backstrap weaving was an INLAY technique, when it is a PICKUP technique. I had a great deal of difficulty with this. The 2 colors, light brown and dark brown, were very close in value, and in the less than ideal light I couldn't see them very well. In addition, the threads were very thin. You need fingernails (or a tweezers!) The next day I rigged up a light and brought my magnifier that I use for Cross Stitch, and I could see much better. Most of us in the class had "visual issues" in that we're not Spring Chickens any longer, and need brighter light, and either larger threads, or a magnifying glass (my son has to read me instructions off of over the counter meds--the print is too small)
The shed stick is below the heddles (toward the weaver). At this point, you need to "strum" or "fluff" the threads so they separate easily and don't break when you use the beater stick. The motion is like plucking harp threads (I'm sure you've all plucked harp threads, right?)
If you look closely, you can see the crossed threads right above Alex's left hand What you don't see before this picture: putting the warp thread through, and then pulling towards you with the stick to seat the thread. It won't actually be encased until you change sheds, as below: lift the rope, and insert the stick.
Strum the threads until you can place the stick in the shed on the other side of the heddles, beat in the previous weft thread tightly, and then run the weft thread through, beat again. Change sheds by pulling the rope down and heddles up.....repeat. This is just for plain weave. For pickup, after you make a nice shed but before you run the weft through, you have to pick up your design. Sigh. I got REAL GOOD at unweaving. Enough said. It's much harder than I thought, and I have infinite respect for the artists who still do this. Alex uses a 2 harness loom that uses some of the backstrap loom and some of the floor loom. It is set at an angle, so instead of looking down at a flat weaving surface, it looks more like a drafting table at a 30-45 degree angle.
Recommendation: for the first project, use 5/2 or 3/2 mercerized cotton. We had wool, and it was very sticky trying to get a clear shed. Perfect your technique before using your handspun!
Dyes, next bit.
Monday, July 17, 2006
To dye for

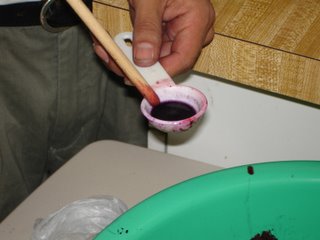

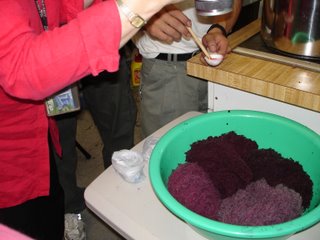

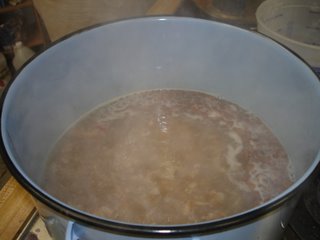
Add your mordant and watch the water turn blue as if by magic
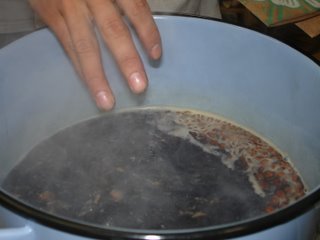



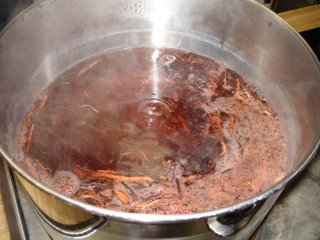






Aaahhh....fun times
More fun times ahead--I'm on the way to Penland School of Craft for a 2 1/2 wk class with Deb Menz on designing yarn. Post in about a month!
Sunday, July 16, 2006
and all the rest







I also had lectures on clothing of the 18 & 19th century, but since I have done a bit of reenacting I didn't pick up a lot of new information. Saturday was spent listening to woad dyeing and spinning for wrinkle resistance. Both very informative. I took a class in dyeing with shaving cream. J & D were in the class with me. The supply list should have listed a biohazard suit. It was the biggest mess. Blue hands for days. When we washed out the excess dye in the bathtub, it looked like a slaughterhouse. Out of 25-30 pieces, only 1 turned out well. No pics on these. Next up: a 3-day workshop on backstrap weaving and natural dyes from Peru. Si habla Espanol? You can probably guess I don't.