Monday, July 17, 2006
To dye for
Cochineal tutorial: I forgot to take pictures of the bugs. We ground them up with a mortar & pestle like Alex does at home, and boiled for 30 minutes or so. Alex is showing us how the dye bath changes color with the addition of citric acid.
And another color with alum
With cochineal he uses copper sulfate, alum and citric acid. If they don't have citric acid at home he uses a lemon, quartered in the dye pot. The copper and alum are found near his home as crystals in the earth. He also finds iron there too. He uses just a pinch (maybe 1/8 tsp). He adds the yarn in dry, unmordanted.
Colors in the basin: he gets the different depths of color by the length of time in the dye pot. They have been "dipped" twice: once without mordant, and then the mordant is added to the pot and the skeins dipped a minute or less to set the color. Then he plunges them into COLD water--no concern about shocking the wool. He WRINGS it dry.
The next dyepot is with the seed pods of tarak (tarok--I googled both spellings but couldn't find any dye info) These are the pods. They resemble locust beans. Shred up the pods. (This photo looks like severed fingers)
And place into boiling water for 30 minutes
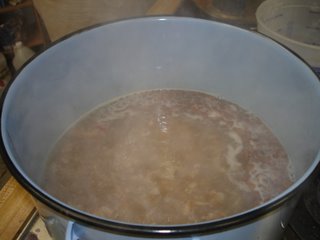
Add your mordant and watch the water turn blue as if by magic
He uses iron sulfate and alum and blends them with his high tech equipment
This yarn is added wet. The color here is not true--it was more purple than that--very much resembled the colors you get with logwood.
The last bath was from masicopa, which is a root similar to madder. His family hikes up into the mountains to harvest it. The mordant here is ash from 2 trees that don't grow here, one a type of pepperberry tree. The wool is added dry. At home, they keep the bath overnight and redip in the morning. This slowly reacts with air, similar to the way indigo does, to deepen the color.
Dye pot is orange-red
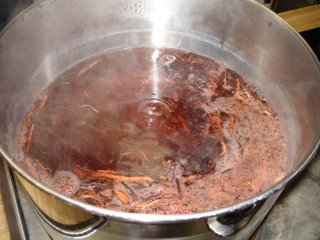
Here you can see bits of root sticking to the yarn. In all the baths, he did not strain out the vegetable matter
Between dips. The second dip was in walnut leaf water. In Peru there is a plant he calls "nogalo" (quotes are because I don't know how to spell it!). In English, he was calling it walnut. Now, we are all familiar with using black walnut shells/husks for brown dye, but he uses "walnut" leaves as a tannin source. One of the women in the class had a walnut tree, so they (he and the interpreter) went over to her house to collect leaves. He says it is not the same--they smell different! And when we boiled it, the water was a paler yellow than he is used to with his walnut. However, when the yarn was dipped into the walnut water, the color darkened! He says the color is guaranteed for 2000 years.
Again, the different shades are from different lengths of time in the bath.
I was fascinated by how different his instructions were from most everything else I had read, or had heard in other classes. He was very specific about the volume of water; I have always read/heard that the volume did not matter; it was the amount of dyestuff and amount of fiber. We have been told to make sure our yarn is thoroughly wet; he adds his dry, and unmordanted. We measure mordant by weight of goods, he uses a pinch. And, apparently, both ways work. I'm now convinced there is NO WAY to screw up natural dyeing.
And last but not least, we each got a handmade Andean spindle and a ball of alpaca to spin.


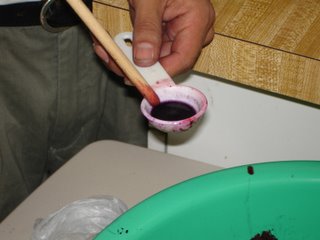

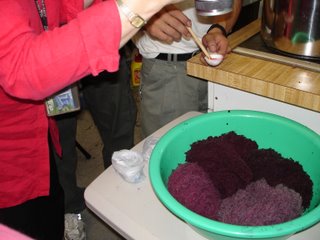

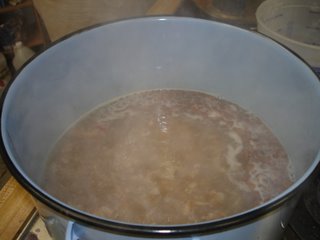
Add your mordant and watch the water turn blue as if by magic
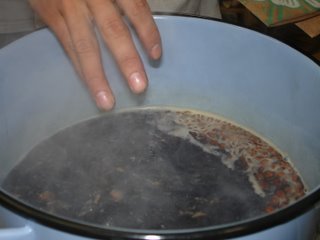



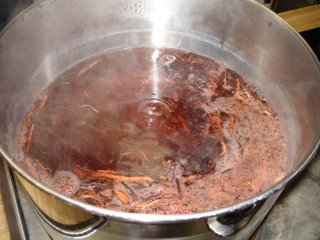






Aaahhh....fun times
More fun times ahead--I'm on the way to Penland School of Craft for a 2 1/2 wk class with Deb Menz on designing yarn. Post in about a month!